26 Nov 2023 09:37 - In evidenza
Andrea Contin: «I vantaggi per l’ambiente del Biochair, il carbone vegetale»
Al Centro di Ricerca di Marina di Ravenna c’è un laboratorio, nato dalla collaborazione tra Unibo e Fraunhofer Institute Umsicht, che si occupa dello sviluppo di materiali innovativi come il Biochair che trova applicazione in diversi ambiti, dalla depurazione alla fertilizzazione.
di Roberta Lodisco
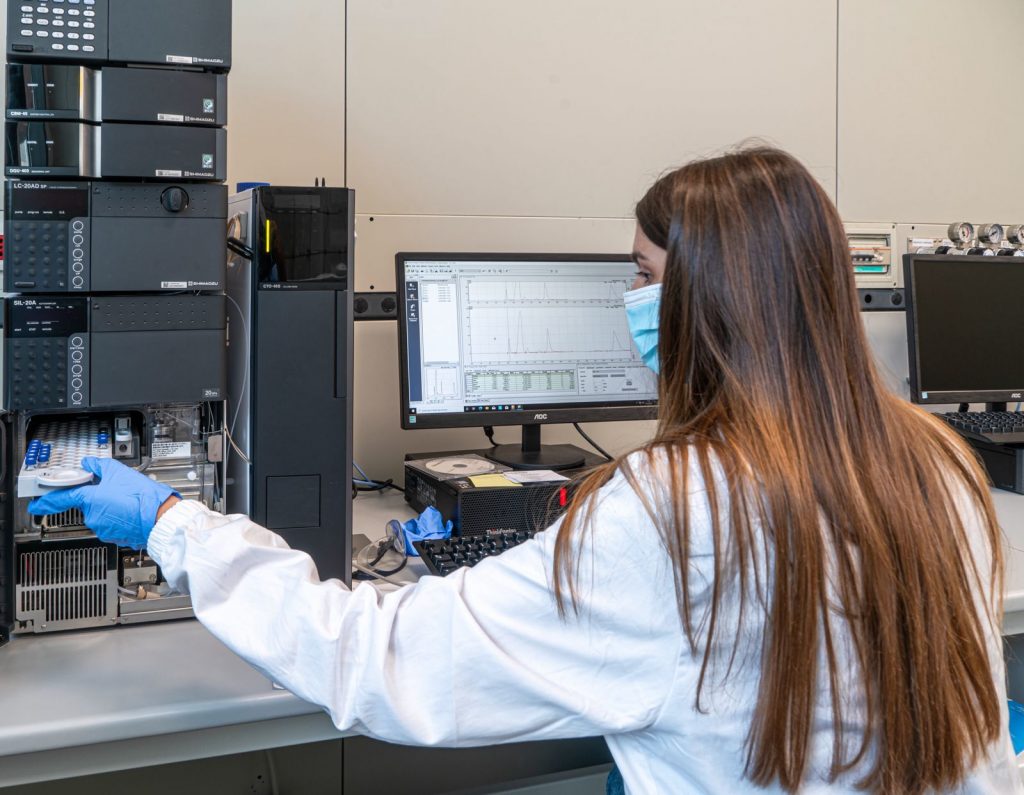
Dalla ricerca al mercato il passo è breve ma non semplice, e lo dimostra il lavoro del “Fraunhofer innovation platform on waste valorisation and future energy supply”, istituito al Centro di Ricerca di Marina di Ravenna (FIP-WE@UNIBO). Il laboratorio, nato dalla collaborazione fra l’Unibo e il Fraunhofer Institute Umsicht, si occupa di ‘produrre conoscenza’ sviluppando materiali innovativi, a prevalente matrice carboniosa, sfruttabili nel campo della sostenibilità ambientale. Infatti i prodotti creati in laboratorio trovano applicazione nel campo energetico, del riciclaggio, della depurazione, della fertilizzazione, della raffinazione e della bonifica dei suoli. A spiegare il progetto è Andrea Contin, direttore del team di ricerca e professore ordinario di Fisica all’Università di Bologna.
Cosa fate nel vostro laboratorio?
«’Produciamo conoscenza’. Sembra una frase fatta ma in realtà è esattamente questo che facciamo. Come laboratorio cerchiamo di realizzare dei prodotti che possano passare dall’università al mercato vero e proprio, entrando in un circuito che ne valorizzi le conoscenze».
Di cosa vi siete occupati principalmente?
«Ci siamo concentrati su materiali che hanno una duplice funzionalità di tutela ambientale. Da una parte produciamo dei carboni utilizzando materiali di scarto, favorendo lo sviluppo di un’economia circolare, dall’altro, utilizziamo questo particolare carbone per purificare le acque e i terreni. Dall’assorbimento di queste sostanze otteniamo un secondo prodotto, utile alla fertilizzazione dei suoli».
In che modo date vita a questo particolare materiale?
«Siamo partiti dalla carbonizzazione degli scarti legnosi, con un processo chiamato pirolisi, ovvero il riscaldamento ad alta temperatura senza ossigeno. In questo processo una parte delle sostanze evapora, lasciando un residuo solido, simile alla carbonella, e prende il nome di Biochar».
Quale è la differenza con la carbonella comune?
«I materiali utilizzati. La carbonella commerciale è prodotta con legno nuovo, noi utilizziamo scarti, come le potature».
Quale è la caratteristica principale di questo materiale?
«È estremamente poroso, funziona come una spugna che assorbe qualsiasi cosa. Così abbiamo pensato di sfruttare questa caratteristica. Abbiamo modificato il prodotto in modo da renderlo più efficiente e sfruttarlo, ad esempio, nell’assorbimento di azoto dalle acque di scarico dei depuratori. In questo modo recuperiamo delle sostanze nutrienti e le concentriamo in un cristallo, composto da magnesio, fosforo e azoto chiamato struvite. È un fertilizzante a rilascio controllato».
Ora che avete creato questo nuovo prodotto, quale sarà il suo futuro?
«Adesso l’obiettivo è immettere il brevetto nel mercato. Per noi la cultura è proprio il creare una ricetta per produrre qualcosa di nuovo, ma ovviamente, l’università non ha le capacità produttive per dare vita a tonnellate di questi nuovi materiali. Speriamo che qualcuno possa interessarsi alla cosa. Promuovendolo cerchiamo di dare visibilità per un possibile acquisto della licenza così il prodotto entra in produzione e noi, allo stesso tempo, guadagniamo dalla licenza dei brevetti».
Quanti prodotti avete brevettato?
«Al momento due processi. Il primo è quello dal Biochar alla Struvite. Il secondo riguarda lo sviluppo di un carbone modificato da utilizzare nei sistemi di respirazione a circuito chiuso, come quelli dei sub o dei vigili del fuoco. Questi sistemi devono produrre aria purificata dall’anidride carbonica; il ‘carbone’ che ci siamo inventati permette di assorbire il CO2 producendo, di conseguenza, aria nuovamente pulita».
L’università come investe nella valorizzazione di questi brevetti?
«Uno dei modi possibili è la creazione degli Spin Off, società commerciali partecipate anche dall’università, che hanno lo scopo di trovare dei clienti per i brevetti che l’Unibo stessa produce. Abbiamo una capacità molto buona dal punto di vista laboratoriale, siamo in grado di definire i processi produttivi delle nostre invenzioni; tuttavia, sfortunatamente, non abbiamo le capacità di andare oltre. Quindi, parte del nostro impegno è speso anche nel trovare qualcuno che possa essere interessato a produrre su larga scala le nostre idee».
Quanto dura il processo dall’idea al brevetto?
«Ogni cosa ovviamente ha i suoi tempi. Il processo per la produzione della struvite lo abbiamo iniziato nel 2019 circa con una tesi di dottorato e lo abbiamo brevettato nel 2022. Un tempo adeguato per mettere in atto tutta la fase di sperimentazione e test. Bisogna essere sicuri che il prodotto proposto abbia una solidità per l’immissione in mercato. Le aziende non vogliono fare troppo sviluppo, i principi di base devono essere solidi».
Il vostro gruppo da quante persone è composto?
«Siamo 20, di cui 5 sono dipendenti dell’Unibo, gli altri sono ragazzi con assegni di ricerca o dottorati, a tempo determinato. Speriamo di poter un giorno offrirgli un posto stabile in squadra, anche se i posti sono abbastanza limitati. Cerchiamo di partecipare a diversi progetti, come quelli europei, in modo da poter finanziare le borse di questi giovani che lavorano “a progetto”».
A quali progetti state partecipando al momento?
«Siamo coordinatori di un grosso progetto Europeo, il NET-Fuels. Si tratta sempre di applicazioni del processo di pirolisi per la produzione di biocarburanti, Biochar, ecc. Allo stesso tempo stiamo lavorando adun progetto con il Ministero dell’Industria, per sviluppare dei carboni adatti ai super condensatori. Questo lavoro lo stiamo svolgendo in collaborazione con la professoressa Soavi che lavora qui al centro di Marina di Ravenna. Siamo sotto contratto con il Ministero della Ricerca nell’ambito del PNRR, e stiamo sviluppando due progetti regionali del Pr Fesr, finanziati dai fondi europei di sviluppo regionale. I diversi progetti ruotano intono più o meno agli stessi ambiti».
I due brevetti nascono da un progetto interno?
«Li sviluppiamo internamente al laboratorio ma riportiamo queste competenze anche nei progetti regionali ed Europei. Ad esempio, uno dei due progetti Pr Fesr è dedicato alla struvite ma con un metodo di produzione differente».
Come procede la collaborazione con il Fraunhofer Institute?
«Tutto è nato circa 10 anni fa. Nel 2017 mi è stato chiesto, dal loro quartier generale, di immaginare il futuro della nostra collaborazione. La risposta è stata la creazione del centro comune fra il Fraunhofer e l’Unibo. Questo ci ha permesso di avere i soldi per la sistemazione del laboratorio e l’acquisto degli strumenti. Con loro ci troviamo bene, promuoviamo a vicenda le nostre competenze e proprietà intellettuali nei nostri rispettivi Stati. Anche loro fano parte del progetto Europeo di cui siamo coordinatori. Tutto procede bene, il laboratorio e la collaborazione si sono evoluti e abbiamo raggiunto i nostri obiettivi sia dal punto di vista della ricerca che dei fondi raccolti».
Quale è la vostra aspirazione più grande?
«Personalmente direi il poter dare a tutti il lavoro a tempo indeterminato, ma sfortunatamente è solo una speranza. Al momento stiamo cercando, attraverso Università e Comune, di creare uno Spin Off, nell’incubatore che nascerà a Marina di Ravenna, per poter offrire ai ragazzi una prospettiva che non sia di breve termine».